Infill Patterns
The Importance of Infill in 3D FDM Printing
In Fused Deposition Modeling (FDM) 3D printing, infill plays a crucial role in determining the strength, weight, material usage, and print time of a part. Infill refers to the internal structure of a 3D-printed object, which is typically hidden beneath the outer shells (perimeters). Unlike the solid exterior, the infill is a patterned lattice that provides structural support while optimizing material efficiency. The choice of infill percentage, pattern, and density significantly impacts the final printed part's performance.
1. Strength and Durability
One of the primary functions of infill is to enhance the mechanical strength of a 3D-printed object. A higher infill percentage (e.g., 50-100%) results in a denser internal structure, making the part more resistant to stress, compression, and bending forces. This is essential for functional parts such as mechanical components, load-bearing structures, or tools. Conversely, low infill (e.g., 10-20%) is suitable for lightweight decorative items that do not require high strength.
The infill pattern also affects durability. Common patterns like grid, honeycomb, triangular, and gyroid distribute forces differently. For example:
- Honeycomb provides excellent strength-to-weight ratios, making it ideal for aerospace and automotive applications.
- Gyroid offers isotropic strength (uniform in all directions) and is useful for flexible or vibration-resistant parts.
2. Material Efficiency and Cost Savings
Since infill reduces the amount of filament used, it significantly lowers material costs. A fully solid print (100% infill) consumes far more filament than a 20% infill part while often providing only marginally better strength. By optimizing infill density, users can achieve a balance between strength and material economy.
3. Print Time Reduction
Higher infill percentages increase print time because the printer must deposit more material. For non-functional prototypes or display models, a low infill (10-20%) drastically reduces printing time without compromising aesthetics. Conversely, functional parts that require durability may justify longer print times with higher infill.
4. Weight Optimization
Infill allows for precise control over a part's weight. Applications like drones, RC cars, or wearable devices benefit from lightweight structures with optimized infill. A well-chosen infill pattern (e.g., cubic or gyroid) can maintain rigidity while keeping weight minimal.
5. Thermal and Acoustic Properties
Certain infill patterns influence thermal insulation and sound dampening. For example:
- Sparse infill can trap air, providing slight thermal insulation.
- Gyroid infill can help absorb vibrations, making it useful for speaker enclosures or mechanical dampers.
6. Support for Top Layers
Infill provides a foundation for upper layers, preventing sagging or poor surface finish. Without sufficient infill, top layers may droop or appear uneven, especially in large flat areas. A balance must be struck—too little infill causes weak top surfaces, while too much wastes material.
Conclusion
Infill is a critical parameter in FDM 3D printing, affecting strength, weight, material usage, and production time. By carefully selecting infill percentage and pattern, users can tailor prints for specific applications—whether for lightweight prototypes, high-strength functional parts, or cost-efficient production. Understanding and optimizing infill ensures better performance, reduced waste, and faster printing, making it an essential consideration in 3D printing workflows.
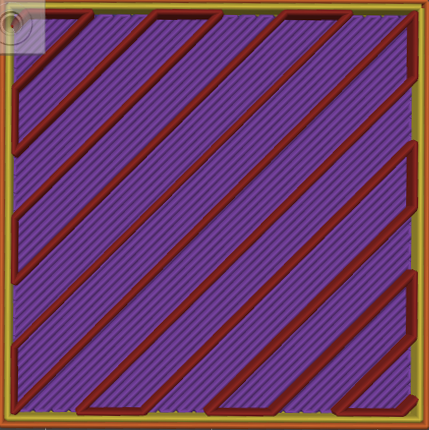
Aligned Rectilinear
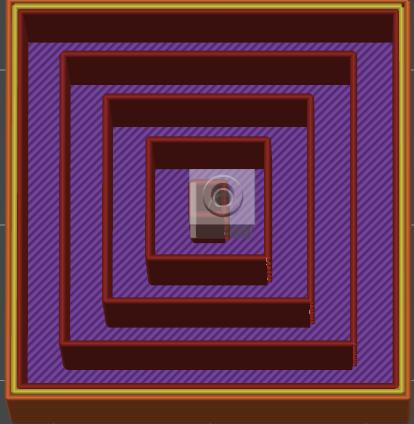
Concentric
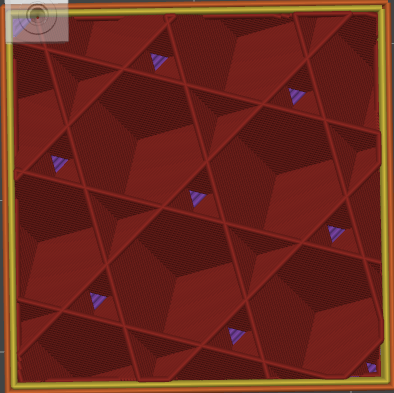
Cube
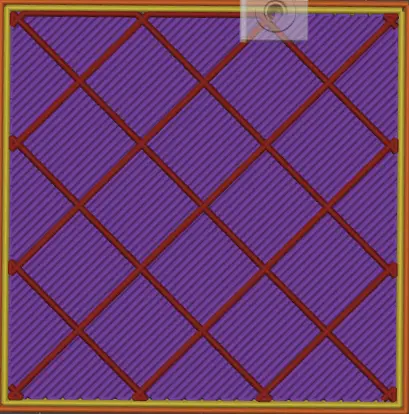
Grid
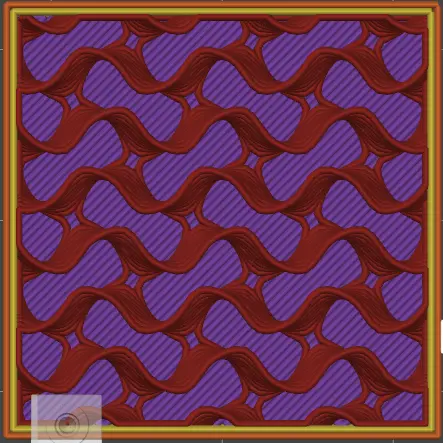
Gyroid
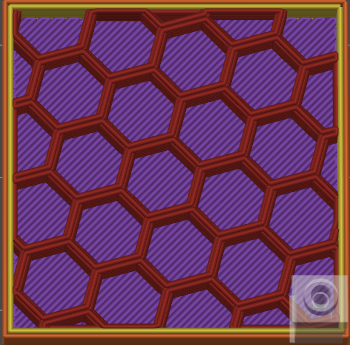
Honeycomb
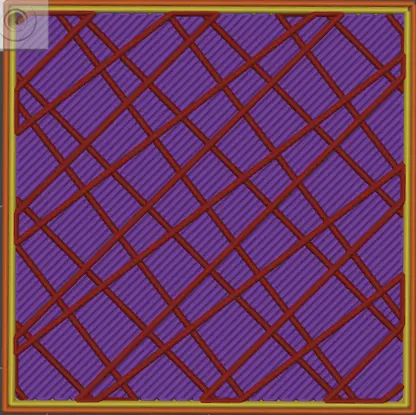
Line
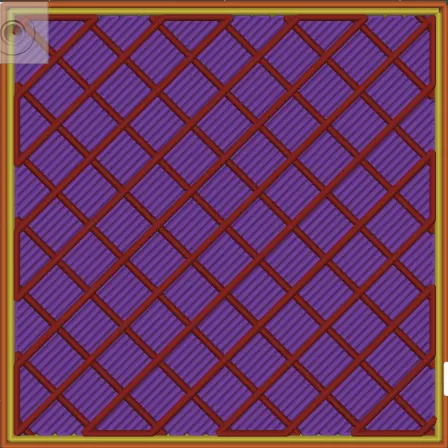
Rectilinear
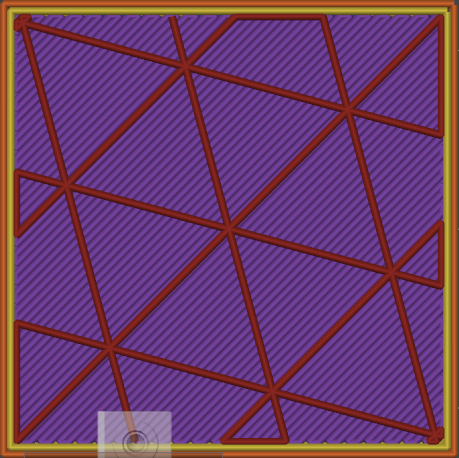
Triangles
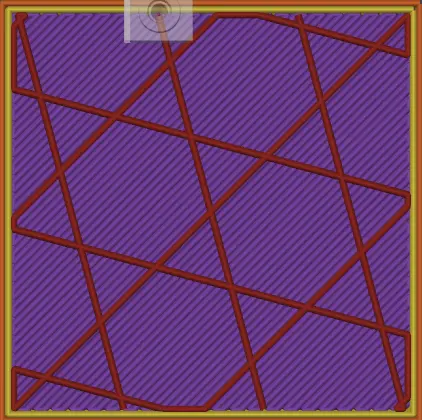